Manufacturing Facility
We continue to invest in equipment, improve product quality, reduce production costs and keep profits to our customers!
Working process
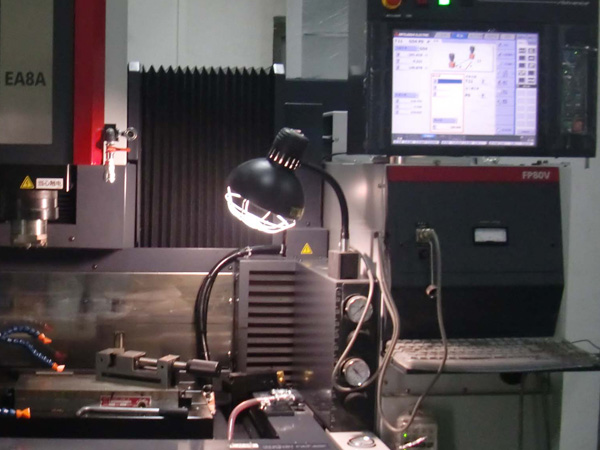
- EDM
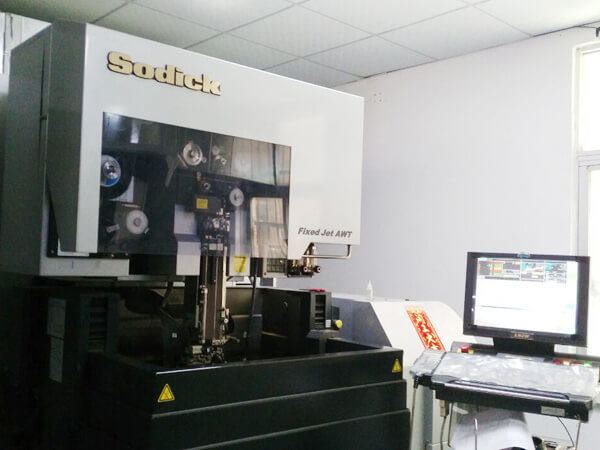
- Wire-cutting EDM
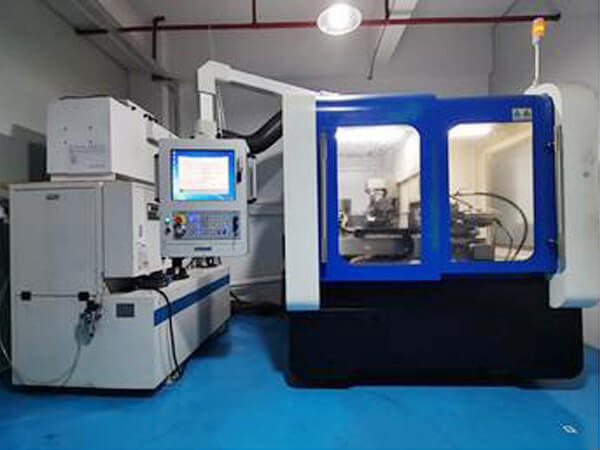
- CNC Grinding
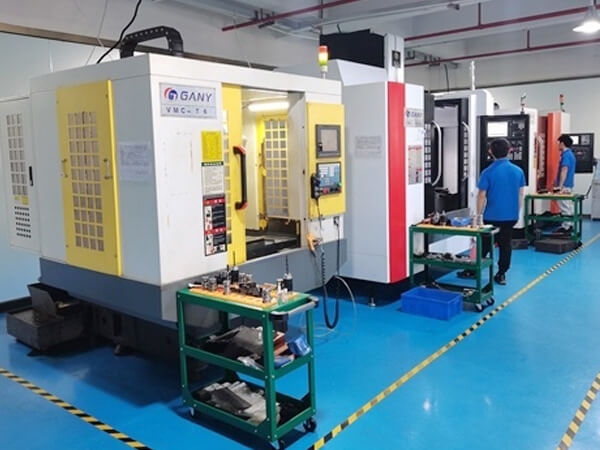
- CNC Milling
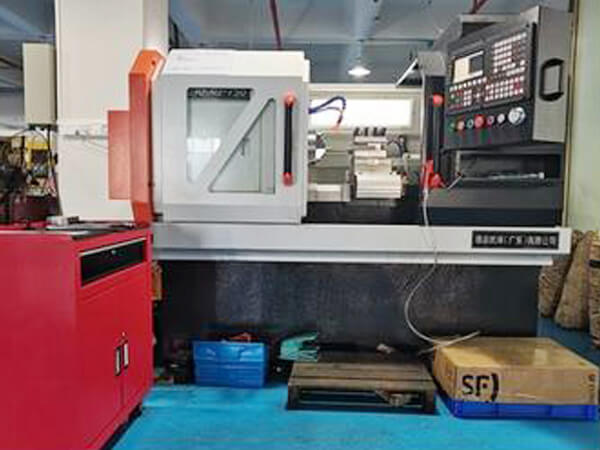
- CNC Lathing
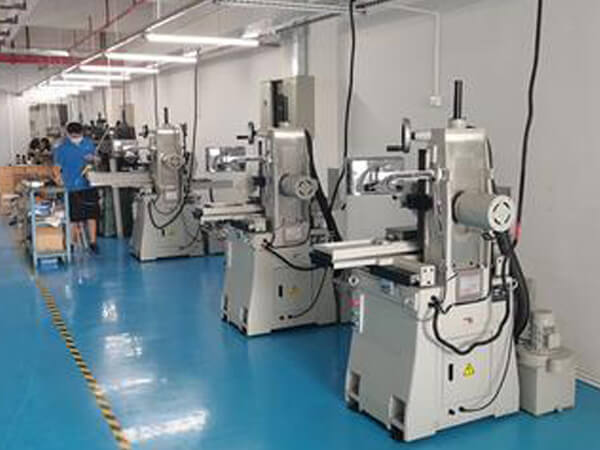
- Plane Grinding
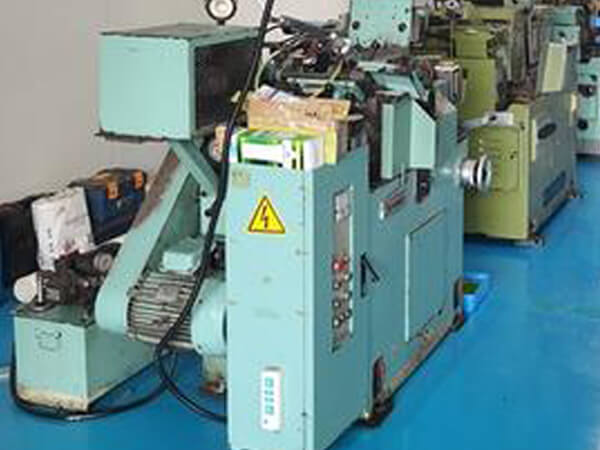
- Centerless Grinding
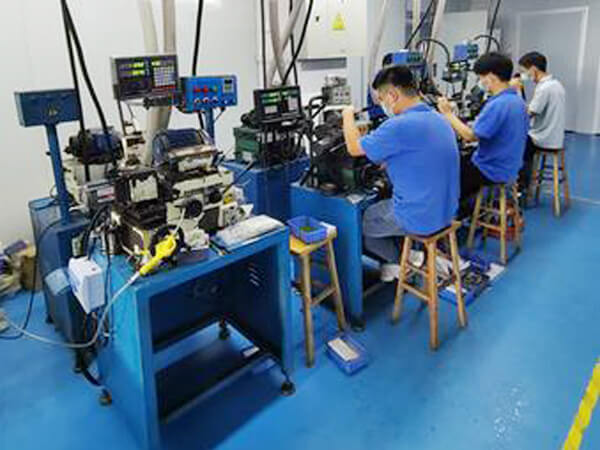
- Punch Forming
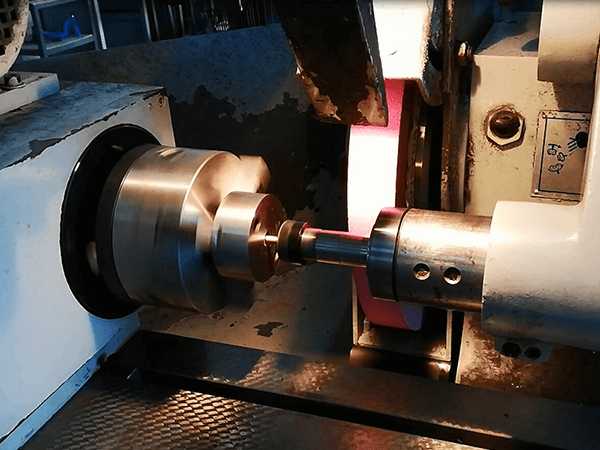
- Cylindrical Grinding
How to choose your materials
There are a wide range of tool steels and stainless steels that can meet the requirements of virtually every application; the challenge is determining the best steel that will optimize your process performance. Specific applications call for many different qualities in tool steels. These qualities are achieved by adding particular alloy(s) with an appropriate amount of carbon. The alloy(s) in combination with the carbon result in wear, toughness and compressive strength characteristics. Steels vary significantly in hardness, wear resistance and toughness.
To determine the Right Tool Steel for your application, see below.
There are a wide range of tool steels and stainless steels that can meet the requirements of virtually every application; the challenge is determining the best steel that will optimize your process performance. Specific applications call for many different qualities in tool steels. These qualities are achieved by adding particular alloy(s) with an appropriate amount of carbon. The alloy(s) in combination with the carbon result in wear, toughness and compressive strength characteristics. Steels vary significantly in hardness, wear resistance and toughness.
To determine the Right Tungsten Carbide for your application, see below.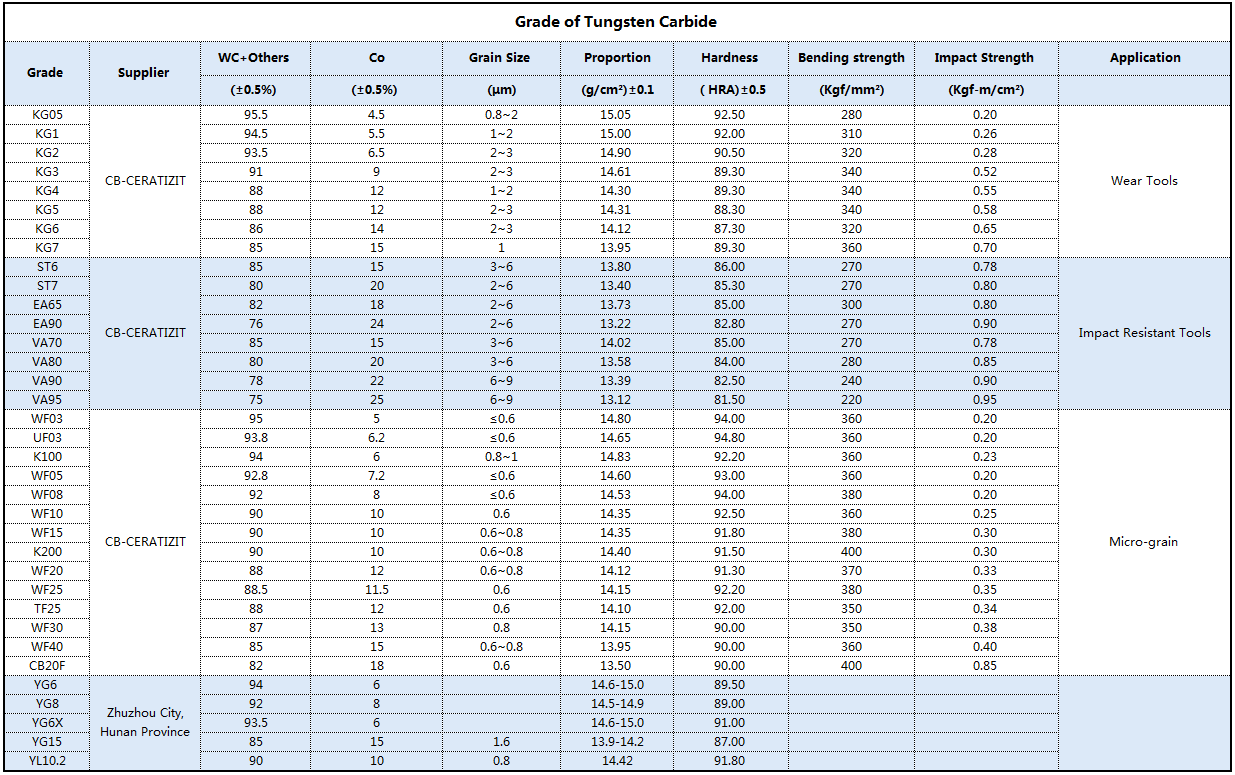
Wear resistant surface treatments offer great benefit to stamping tools when applied appropriately. While there are many good surface treatments and processes to choose from, Physical Vapor Deposition (PVD) coatings are ideally suited and typically the best option to use on precision slip and press fit punch components.
Selecting the right surface treatment and substrate tool steel combination is critical for achieving optimum tool life. PVD coatings provide excellent abrasion and galling resistance while maintaining the integrity of many substrate tool steels. These coatings work best when applied to high speed tool steels such as M-2, PM-M4, and T-15. A few select cold work tool steel grades can also be PVD coated successfully as long as they maintain at least a 60 HRC when tempered at or above 1,000 degrees Fahrenheit.
It is important to note that the PVD process is a line of sight process, which may limit the ability to coat interior contours and features. For these applications, nitriding, which case-hardens all exposed surfaces, is recommended.
Below is a list of standard surface treatments offered by GS Machining Co., LTD.
Additional coatings are available upon request.
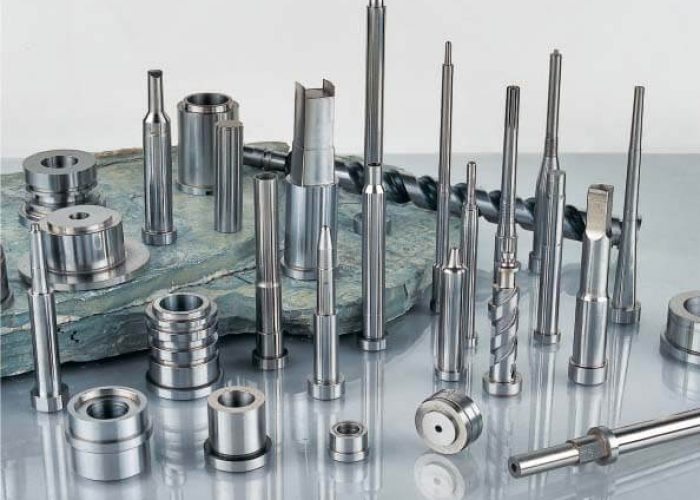